单级泵机械密封的安装质量直接影响设备运行可靠性。本文结合 ISO 21049 标准及工程实践,系统阐述安装全流程,涵盖拆卸规范、部件检查、弹簧比压调整等核心环节,并针对高压工况、颗粒介质等特殊场景提供优化方案。
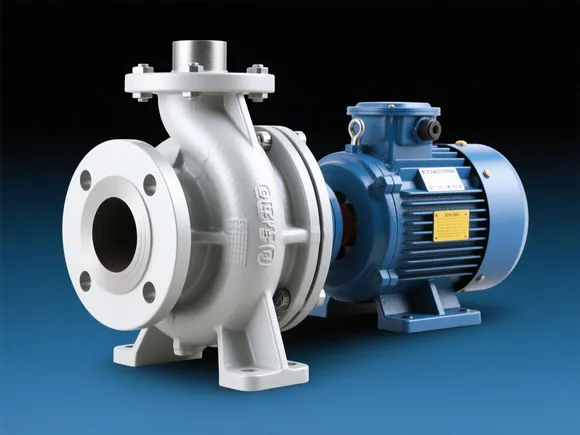
安装前需核对机械密封型号与泵型匹配性,重点关注以下参数:
密封类型:平衡型密封适用于压力>0.7MPa 工况(载荷系数 K<1),非平衡型仅适用于低压场景(K≥1)。
弹簧比压:根据端面线速度调整,低速密封(<10m/s)推荐 1.5-6.0kgf/cm²,高速密封(>30m/s)需控制在 0.5-2.0kgf/cm²。
轴窜量标准:单级泵轴窜量需≤0.5mm,采用百分表测量时,轴向位移偏差应控制在 ±0.05mm 内。
密封组件清洗:使用乙醇或专用清洁剂清除动环、静环表面的防锈油及杂质,确保密封面粗糙度 Ra≤0.2μm。
弹性元件检测:弹簧自由长度偏差需≤±0.5mm,多弹簧结构需保证各弹簧刚度均匀性(偏差≤5%)。
辅助密封圈检查:O 型圈应无变形、裂纹,氟橡胶材质适用温度 - 20℃~200℃,丁腈橡胶仅适用于 - 40℃~120℃。
标记定位:在轴套与密封压盖间做好装配标记,确保回装时轴向位置精度(偏差≤0.1mm)。
无损拆卸:使用专用拉马拆卸动环,禁止敲击密封面。若静环与压盖粘连,可注入少量煤油浸润后取出。
部件归类:将弹簧、密封圈等零件按型号分类存放,避免混淆。
密封面磨损:若动环端面出现环状沟纹(深度>0.05mm),需更换整组密封。
弹簧疲劳:压缩量超过设计值 20% 时,弹簧刚度下降,需及时更换。
轴套损伤:轴套表面划痕深度>0.1mm 时,需采用激光熔覆修复或更换。
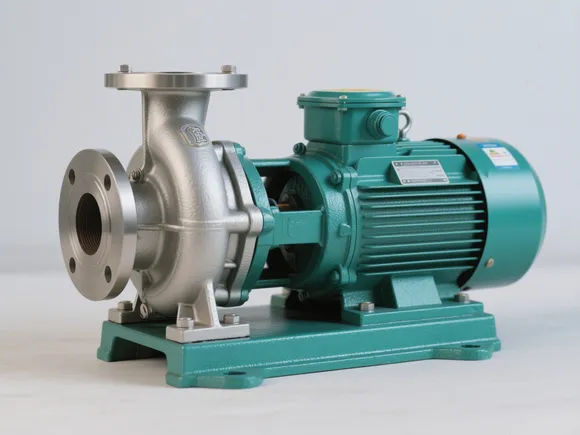
静环安装:将静环压入密封压盖,采用扭矩扳手按 15-20N・m 紧固螺栓,确保静环与压盖贴合间隙≤0.03mm。
动环装配:在轴套表面涂抹二硫化钼润滑脂,将动环沿轴向缓慢推入,确保动环在轴套上的浮动间隙为 0.1-0.3mm。
测量方法:使用卡尺测量弹簧自由长度(L0)与安装后长度(L1),压缩量 ΔL=L0-L1。单弹簧压缩量需控制在 50%-70% 自由长度,多弹簧结构压缩量为 90% 自由长度。
比压验证:弹簧比压 P=K×ΔL/A(K 为弹簧刚度,A 为密封端面面积),需符合设计值(偏差≤±5%)。
压盖安装:将密封压盖对准标记回装,螺栓按对角顺序分 3 次紧固,最终扭矩误差≤±3%。
盘车检查:手动盘车 3-5 圈,检查动环轴向移动灵活性,阻力应均匀无卡滞。
静态测试:通入 0.3MPa 洁净水进行静压试验,保压 5 分钟,泄漏量需≤5 滴 / 分钟。
冲洗系统配置:安装外置冲洗管路,采用 0.5-1.0MPa 洁净水对密封腔进行连续冲洗,流量控制在 3-5L/min。
硬质合金摩擦副:动环 / 静环选用 SiC-SiC 配对,硬度达 HV2500,耐磨性能较石墨材质提升 10 倍。
泄漏类型 | 可能原因 | 解决方案 |
---|
静压试验泄漏 | 密封面划伤、弹簧压缩量不足 | 研磨密封面、重新调整弹簧压缩量 |
周期性泄漏 | 轴窜量超标、转子振动 | 校直泵轴、更换轴承组件 |
经常性泄漏 | 密封圈老化、介质腐蚀 | 更换氟橡胶密封圈、增加防腐涂层 |
端面比压过高:重新计算弹簧比压,必要时更换刚度较低的弹簧。
冷却不足:检查冲洗管路流量,确保密封腔温度≤80℃,否则需增加冷却器。
通过标准化安装流程与针对性优化措施,单级泵机械密封的可靠性可显著提升。严格执行轴窜量控制(≤0.5mm)、弹簧比压校准(±5% 偏差)等核心规范,结合智能化运维手段,可实现密封寿命最大化与维护成本最小化的双重目标。
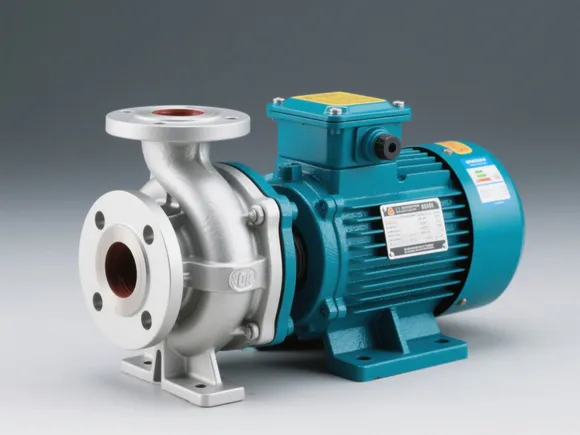
常见问题解答:
问题1:机械密封安装后泄漏的主要原因有哪些?
密封面污染:安装时未彻底清洁,颗粒杂质嵌入密封面导致泄漏。
弹簧失效:压缩量不足或弹簧疲劳,无法维持端面比压。
轴窜量超标:泵轴轴向位移>0.5mm,破坏密封面贴合度。
介质腐蚀:丁腈橡胶密封圈在酸性介质中老化,需更换氟橡胶材质。
问题2:如何延长单级泵机械密封的使用寿命?
定期维护:每运行 500 小时检查弹簧压缩量,每 2000 小时更换密封圈。
优化工况:避免泵抽空运行,控制介质温度≤80℃,颗粒含量<50ppm。
升级部件:高压场景采用平衡型密封 + 硬质合金摩擦副,寿命可延长至 8000 小时以上。
智能监测:安装振动传感器与温度探头,实时预警密封失效风险。